From the stove at home to industrial production
For us to reach our ambitious 2030 sustainability goals, many pieces must fall into place. Engaged employees and a culture of innovation are crucial. A project in Bramsche, Germany, on fossil-free binders is an inspiring example.
Sometimes everything just falls into place. We could not have constructed a better case to show how sustainability, a culture of innovation, employee engagement and living our values together can do great things. It is about how Britta Hinnemann, process engineer, and Maren Potthoff, laboratory specialist, at the conversion unit in Bramsche in northwestern Germany developed a plant-based binder for the Dunicel®range of table covers and placemats.
Started as a game
It all started in 2018 at home in Britta’s kitchen when she made glue with her children. She got the idea that a similar adhesive could be used to replace fossil-based binders in table coverings. It could help Bramsche regain the OK Compost distinction it lost in 2015. “It wasn’t my project, but I really wanted us to have a ‘green’ Dunicel®,” she says. “So I talked to Maren about making an environmentally adapted binder from sugar and flour for our products.” Maren now says, “It had not occurred to me before, but it could work. We have to try it!”.
Tried different plant-based solutions
They started with small-scale tests at home, but soon they were cooking huge amounts of glue that they brought to work. It was obvious that they needed to increase capacity. They talked to their boss and bought a cooker for Bramsche’s lab.
Flour and sugar worked. However, they wanted to simplify the recipe, and when they learned that starch is very common in cardboard manufacturing, they made another trip to the grocery store. “We bought rice, corn and potato starch,” Maren says. “There was a lot of testing before we decided on modified potato starch.”
Started top secret project
After presenting their test results to company management, they were given the go-ahead to start a top-secret project (BRIMA) to develop the binder further. It was so secret that tricky situations often arose . “When someone else came into the room, we had to change the subject. They must have wondered what we were doing,” says Maren.
In 2020, the project invested in an even larger cooker and currently plans to invest in another cooker for industrial production. Britta explains: “It is important that the glue is produced here in Bramsche. It is a biological product that is difficult to store and we want to have control over the ingredients. And yes, the recipe will remain secret”.
Products launched in October
The new binder will be used with tissue from the Group’s Skåpafors paper mill and other ingredients to produce the new material Bio Dunicel®.
Although the project was paused during the pandemic, the result of Britta and Maren’s work – placemats made of Bio Dunicel® – was launched on October 1, 2021. “We’ve been really looking forward to seeing it on the market. It’s been a fantastically exciting development project,” Britta concludes.
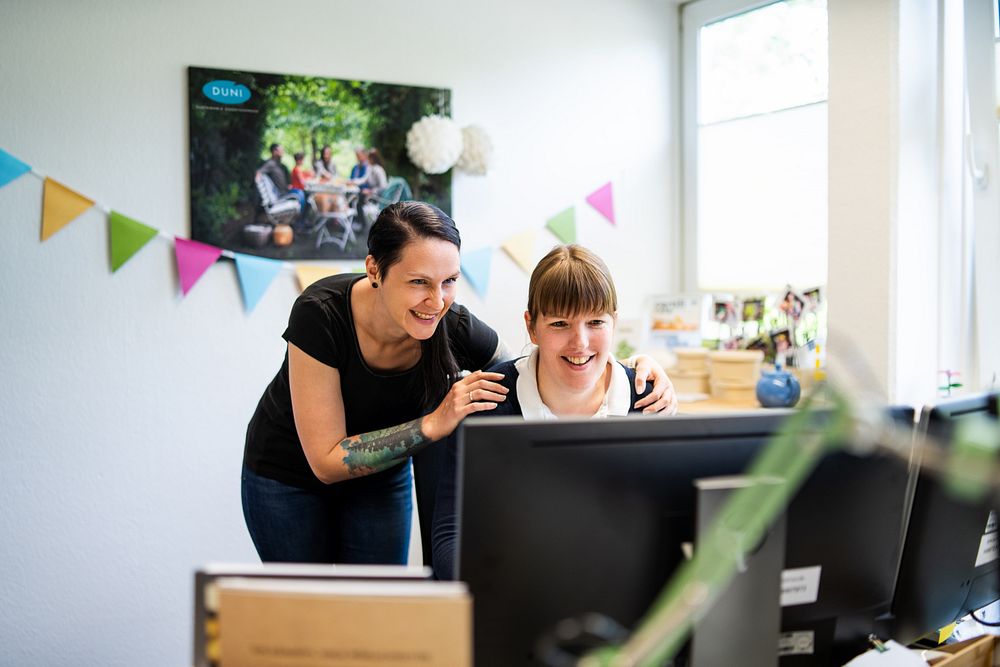
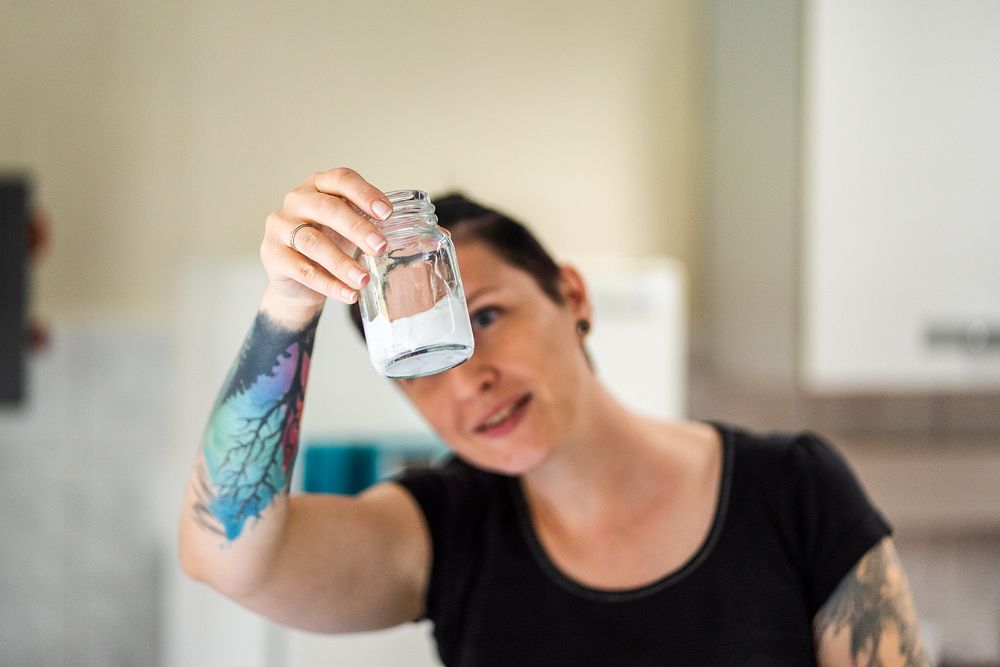
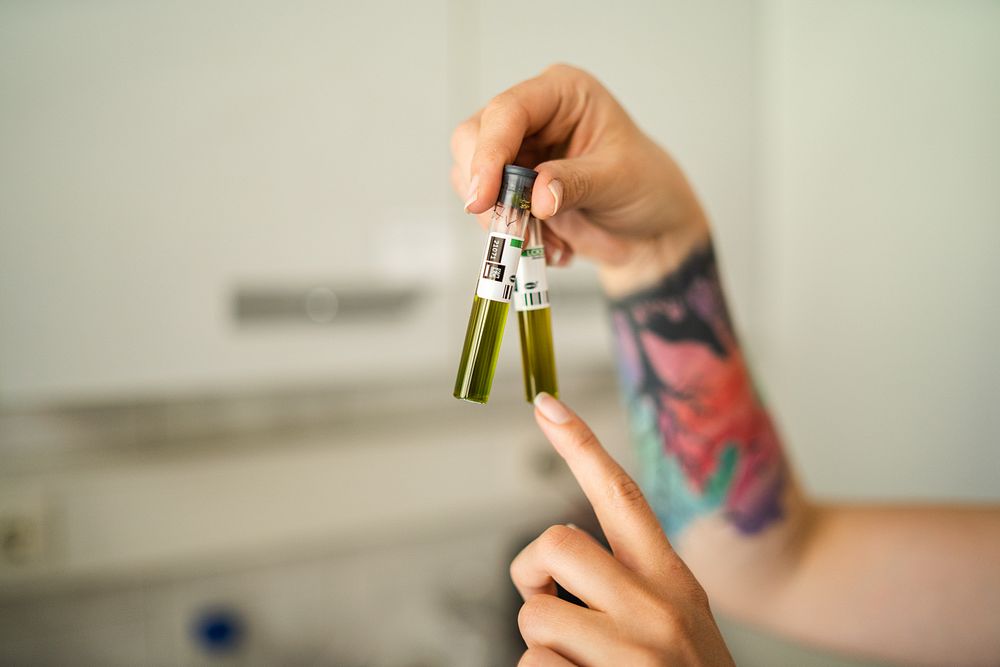